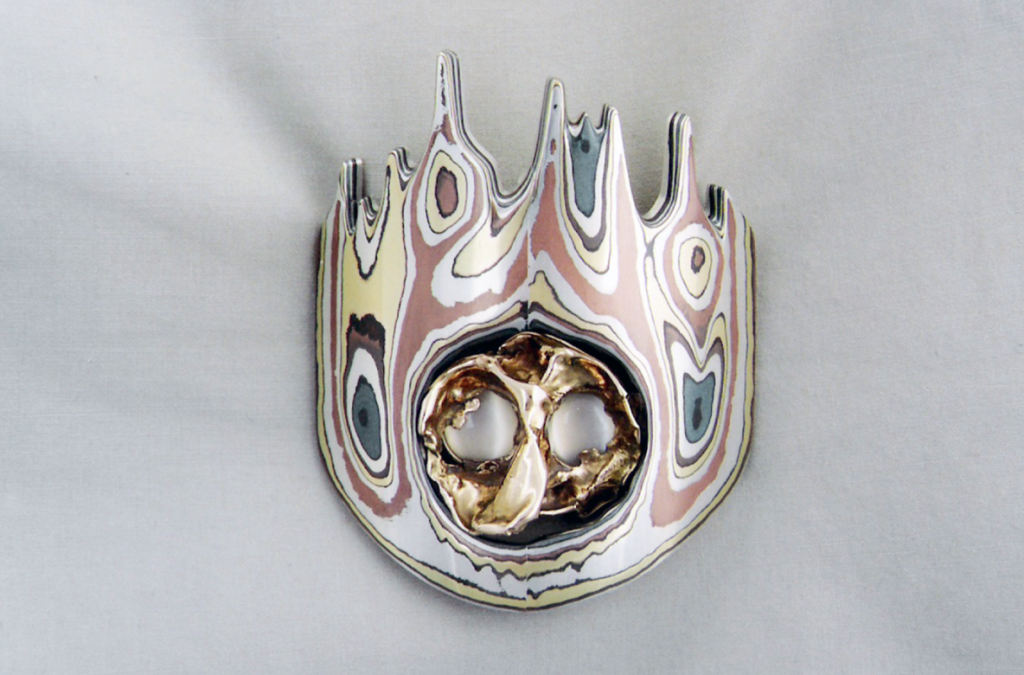
Mokume Owl Pin / Pendant
This is the first mokume gane piece that I made.
In Japanese, mokume gane means "woodgrain metal."
When creating a work with this technique, I want the implication of woodgrain to make sense. For example, this pin/pendant is meant to look like an owl in a hollow tree. The mokume pattern that unfolded resembles weather wood, yet it also appears totem-pole-like and even looks like flames.
The owl-face is a watercasting, created serendipitously by dropping molten metal in water. The face has a scull-like quality — are the moonstone "eyes" signs of wisdom, or are they haunting, or perhaps something sinister? The ambiguities are open to interpretation.
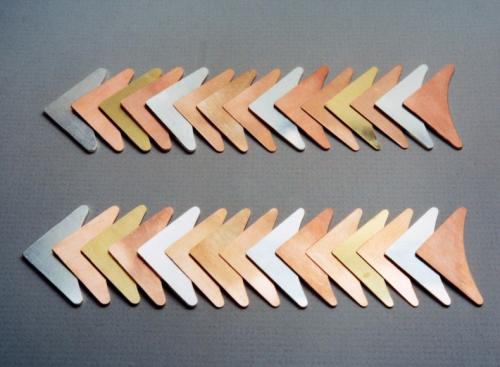
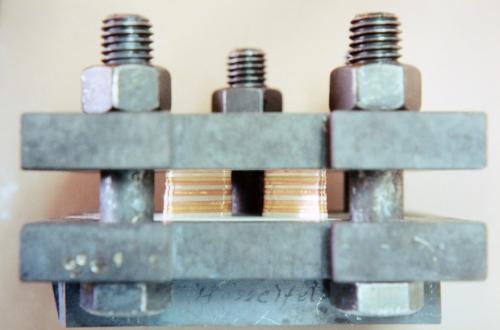
Two rows of fifteen layers of different coloured metals, all perfectly flat and clean. A layer of 18 k. green gold is seen fourth from the right in each row. The other metals are sterling silver, copper, brass, and two copper alloys: shakudo, and shibuichi.
The two sets of fifteen layers are stacked and bolted tight between steel plates while pressed under hydraulic pressure.
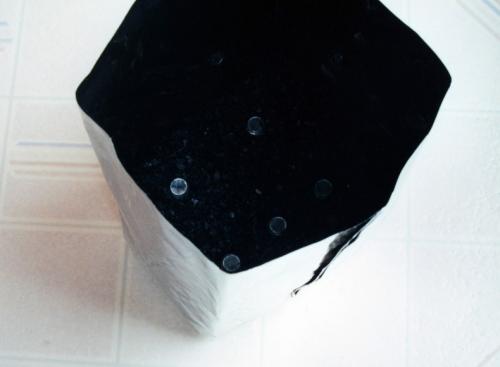
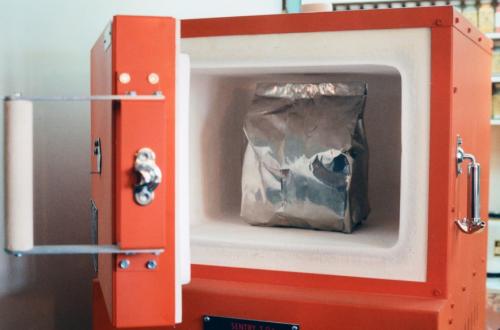
The entire assembly of stacks and bolted steel plates is embedded in charcoal inside a stainless steel foil bag. When sealed, the interior of this bag will maintain a reducing or non-oxidizing atmosphere.
The filled, sealed bag is placed in a digital kiln and heated at about 1400 degrees fahrenheit for 14 hours. The temperature is held just below the lowest eutectic alloy melting point that results between the layers. Literally, under heat and pressure, molecular growth between the layers fuses the stacks into solid blocks.
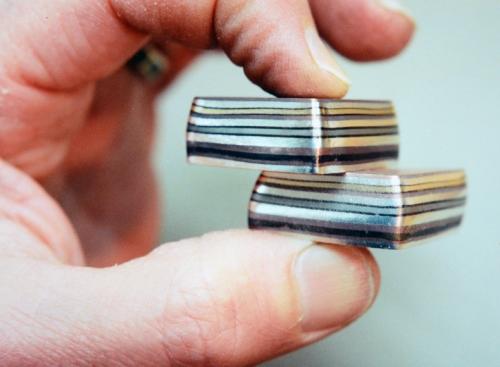
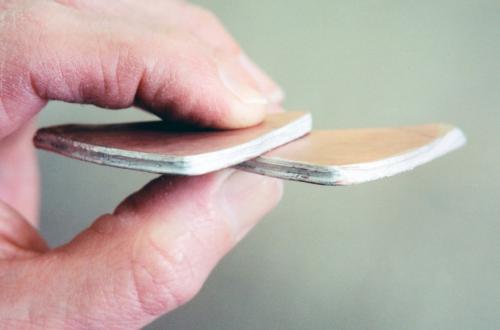
The fused stacks. The edges are filed flush, and the contrasting colours of the metals are temporarily enhanced by being patined in ammonia fumes.
The stacks, smithed out like pancakes, are now heavy sheets. The edges have been coated with solder. All the contrasting layers of metal are still contained within the mokume.
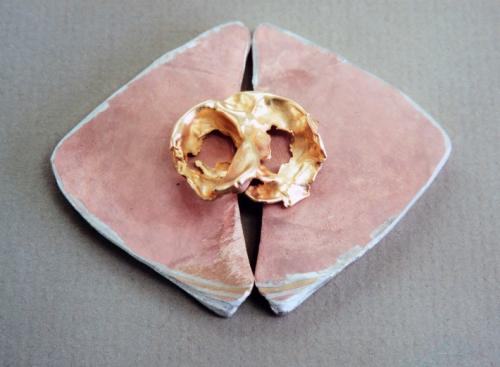

Placed upon the two sheets is a 14 k. yellow gold watercasting (the random result of dropping molten metal in water). While being smithed, some of the internal mokume layers have become exposed at the surface (lower corners).
The two triangular mokume sheets are filed flush along their longest length and soldered together edge to edge. A single sterling sheet also backs the joined mokume shape (not obvious in the photo).
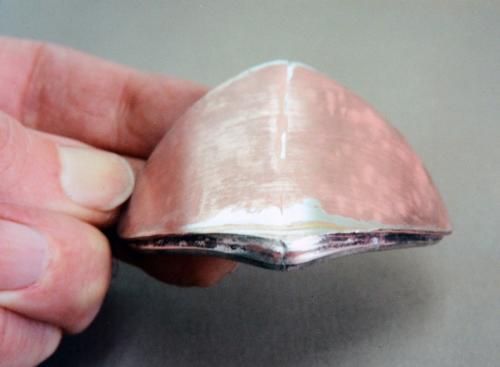
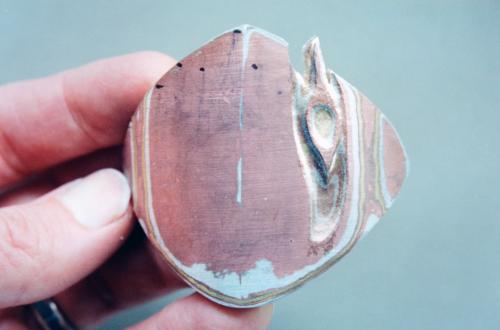
The resulting unit is bent into an arc like the contour of part of a hollow tree.
Revealing the pattern. The two areas of pattern near the corners were created by filing through the layers and hammering them smooth. In another area, the layers are carved into and exposed. The process of partially cutting back the top edge of the piece is also beginning and is intended to create the random-edged look of the top of a weathered hollow tree.

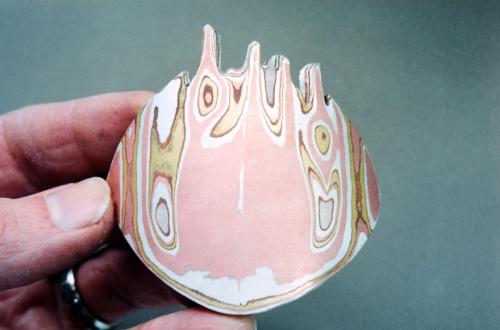
More carving into the mokume to reveal pattern. More random edge along the top is cut away while the higher points are actually bent up beyond the original edge. During this bending, the bond between the mokume layers remained 100% strong.
The pattern is shown smithed flush.
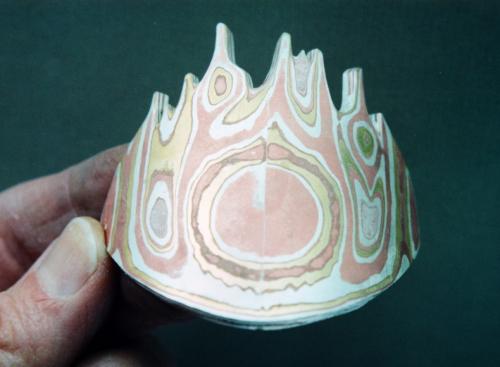
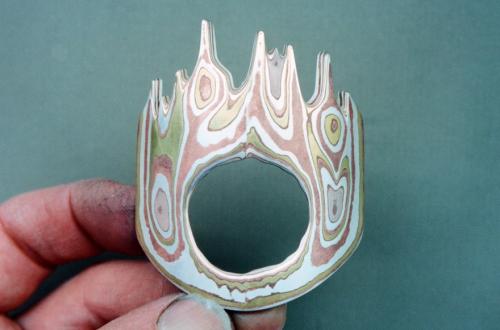
More pattern established around the area that will become the "owl's hole in the tree" and smithed flush. The random edge along the top is finished.
The right and left corners are trimmed away, the hole is cut out, and the remaining surface is smoothed.
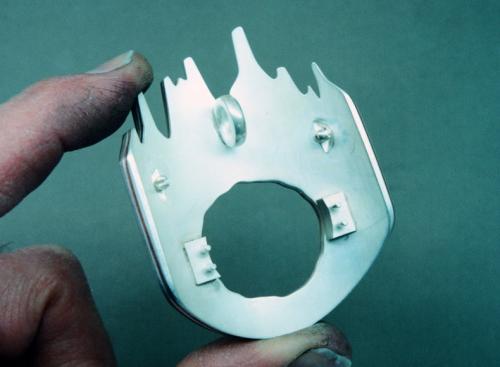
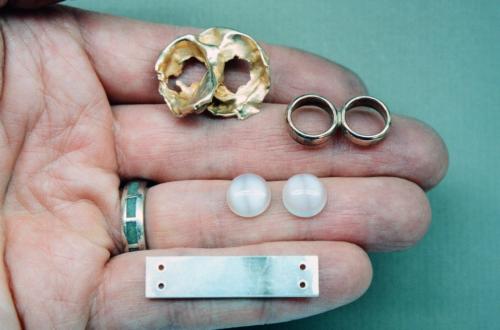
The back is prepared with rivets that will eventually secure the assembly that holds the "owl's face." The hinge and catch for the brooch pin are soldered in place, and the loop for chain is also soldered in place.
Components for the "owl's face" assembly, from top to bottom: the 14 k. yellow gold watercasting, the framework for the two moonstones, the pair of moonstones, and a back-plate with rivet holes.
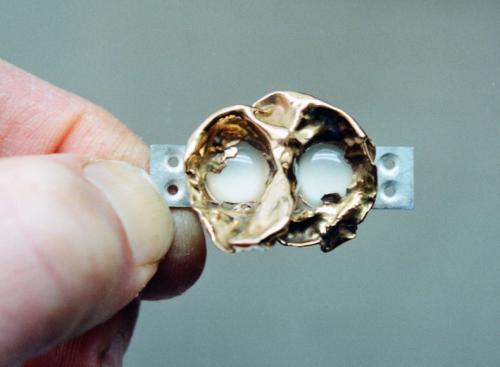
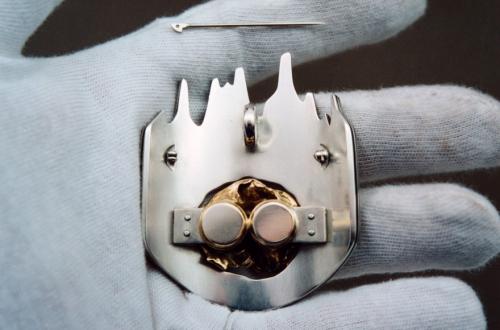
The completed "owl's face" assembly.
The assembly ready to be riveted in place. Sterling circles behind the stones were bezel set from the back to lock the stones in place.
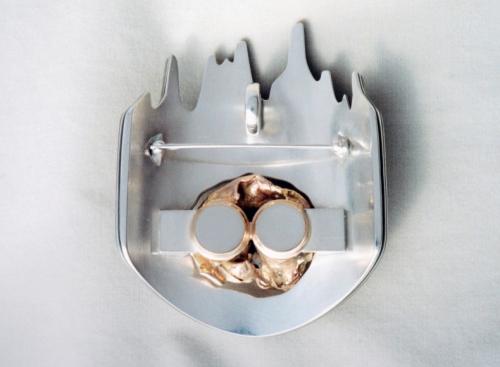
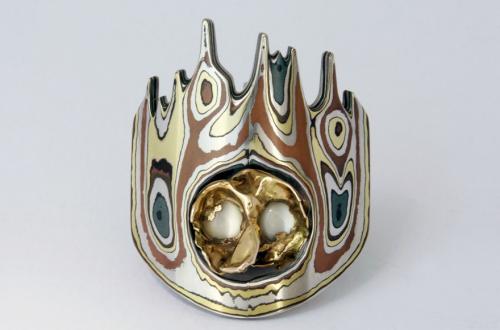
The finished back, riveted and cleaned up, and the brooch pin riveted into its hinge end.
The finished piece. The surface is smoothed to a bright satin, and the mokume is patined using ammonia fumes. The gold and sterling colours remain unchanged, the copper becomes a rich chocolate
brown, the shakudo (96% copper and 4% gold) turns a rich plum-black, and the shibuichi (85% copper and 15% silver) turns turquoise-gray, (the brass never became visible). The patined mokume is sealed with 20 coats of Johnson's floor wax.